SF200 secondary high frequency inverter welding soldering power supply adopts high speed DSP+CPLD system construction design. which makes the soldering process more easier, faster, and stable. Frequency is 1kHz, when compre with 50Hz power supply, the current adjust process is more accurate, heat speed has been improved, welding time declined. Its output current is close to DC, the heat is concentrated, the plastic ring is well formed, the welding spatter is greatly reduced, and the weld nugget consistency of the solder joint is good.
When compared with ordinary industrial frequency controllers, this intermediate frequency DC welding controller has the following advantages:
1. The current flowing in the secondary welding circuit is direct current, and the inductive reactance in the secondary circuit produced by the different immersion depths in the welding workpiece greatly reduces the influence on the welding current;
2. The mass of the welding transformer is greatly reduced, which not only realizes the integration of the transformer and the welding tongs, but also helps to reduce the overall weight of the robot welding tongs;
3. Various communication protocols, such as RS485, RS232, CAN, can be applied to the communication between the welding host and the upper computer (or robot), and personalized communication modules can also be configured according to user requirements;
4. It can weld materials such as aluminum and galvanized metal, and the welding result is good;
5. Especially suitable for three-layer board welding, welding of very thin materials and precision welding requirements;
6. The control of current improves the quality of solder joints and reduces spatter.
The welding controller has a strong information processing capability, an adaptive function is added to the control system, and the adaptive space is large. One welding tongs can adapt to the welding requirements of plates of different thicknesses in one station. It has a wide application field and can be adapted to ordinary Welding of cold-rolled sheet, galvanized sheet, hot-formed sheet, high-strength sheet and aluminum sheet.
I. Application
Welding material: ordinary carbon steel plate, galvanized plate, high strength plate, stainless steel plate;
Welded ordinary steel plate thickness: ≥0.4mm;
Zinc layer thickness of galvanized sheet: 15-25μm;
Specifications of welding screws: M3 ~ M12;
Stud diameter/workpiece thickness ratio: ≤8:1;
Welding speed: 20-40 pcs/min;
II. Technical parameters:
1. Power supply voltage: three-phase 380V 50HZ/60HZ, power fluctuation +15%, -20%
2. Output voltage: single-phase PWM output 500V
3. Welding current range: 100A~2500A
3. Welding time range: 6mS~100mS
4. Heat dissipation method: forced air cooling
5. Working environment temperature: -20~60℃
6. Working environment conditions:
Ambient temperature: -20℃~ 60℃
Relative humidity: ≤ 90%RH (no frost)
Indoor installation: no flammable, explosive, corrosive gas, no conductive dust, vibration less than 0.5G
The altitude is lower than 3000 meters, over 3000 meters should be used with a lower capacity level
7. Dimensions: 240 * 160 * 50mm Hole size: 225 * 145mm
8. Control board weight: 0.8KG
9. Dielectric strength: 3500 VRMS
III. Main features:
1. Output power frequency: 1KHZ, time accuracy is ms level;
2. Programmable up to 16/32 sets of welding specifications, 16 sets of fixed point mode, 32 sets of robot mode;
3. Three-stage heating process: preheating, welding, and tempering; in the welding section, you can define the increasing and decreasing sections by yourself;
4. Programmable output I/O port: programmable 3-segment output, better adapting to PLC, robot, etc.;
5. It has the function of counting solder joints.
6. The inverter control power supply is adopted, the control is precise, and the output current is stable;
7. Digital setting of welding current and welding time;
8. The terminal display of the welding machine adopts a touch screen, which can display and monitor all important operation results and preset parameters in real time;
9. When the welding parameters deviate from the set value, the system has self-diagnosis function and automatic alarm function;
10. All welding parameters such as welding current and welding time can be directly set through an external programmer;
11. Each controller can be equipped with up to 2 programmable welding interfaces, each interface can be programmed separately, and 2 interfaces can meet simultaneous welding;
12. With anti-repeat welding device;
13. With overload and short circuit protection device;
14. With temperature monitoring protection;
15. With power-saving control circuit to reduce no-load loss;
16. The welding voltage and current have a unified adjustment function;
17. Provide welding machine parameter performance monitoring software;
18. Provide IO mode counting alarm function and interface;
Relevant peripheral accessories and products:
STP30 Constant Voltage Feedback Module;
STP10 RC Absorption mModule;
STP20 Three Phase Synchronous Transformer Module;
STP22 6 Pulse Trigger Module;
STP01 LCD Operation Display Screen Module;
SFP20 IGBT Driver Module。
>> More Accessories
>> Return
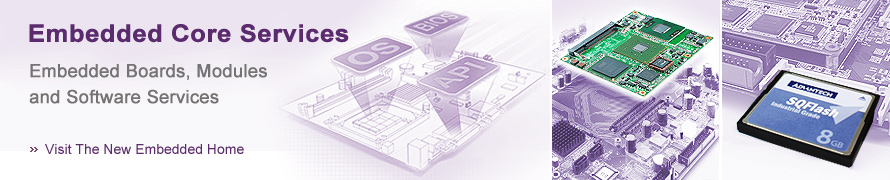
------------------------------------------------------------------------------------------
If you want to buy our products, you can easily contact us by the following two ways:
1、Welcome to Sinepower Sales Consulting Hotline: +86 18938061832;
2、You can also fill in an online consulting form to tell us some of your information. The more we know about you, the more thoughtful service you can be provided.
If you encounter with some problems in the using process, please use QQ online to communicate with us, you can also email sales@sinepower.cc for feedback!